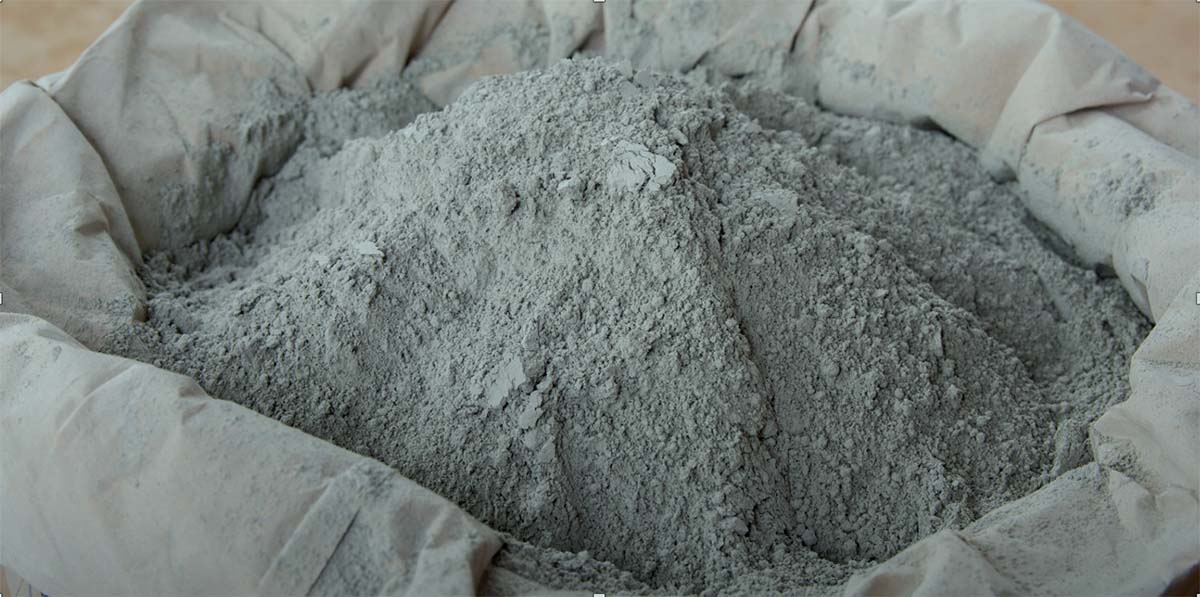
The Best Methods for Efficient Powder Milling
Getting the right particle size can make or break a product. If your powders aren’t the right size, they won’t mix, dissolve, or perform the way they should. The right milling method saves time, reduces waste, and improves quality.
In this guide, the experts at M&M Milling will walk us through the best powder milling methods and how to get better results.
Powder Milling Overview
Powder milling is the process of grinding raw materials into fine powders, often used in industries like ceramics, pharmaceuticals, and chemicals. It uses techniques (such as ball milling, jet milling, or hammer milling) to break down larger particles into smaller more uniform sizes.
It’s incredibly necessary for product consistency, reactivity, and processing efficiency.
Here’s Why Particle Size is Important:
- It affects how powders flow and mix.
- It changes dissolution rates in pharmaceuticals and chemicals.
- It impacts overall product quality and performance.
Ever wonder why some powders clump while others pour smoothly? It all comes down to particle size control.
So, let’s take a look at how different milling methods make that happen.
Common Powder Milling Methods
Different milling techniques control particle size in different ways. The best method depends on the material, production scale, and desired outcome.
1. Air Classifying Milling
Best for: Fine powders with tight particle size distribution
How it works: Combines impact milling with air classification to separate fine and coarse particles automatically.
Expert Tip: Ideal for heat-sensitive materials since it generates minimal heat.
2. Ball Milling
Best for: Producing fine and ultra-fine powders
How it works: Rotating balls impact and grind materials in a chamber.
Example: Used in battery material production for uniform particle sizes.
3. Roller Milling
Best for: Large-scale processing of bulk materials
How it works: Uses counter-rotating rollers to crush and size materials consistently.
Advantage: High output with minimal energy waste.
4. Jet Milling
Best for: Ultra-fine powders with precision control
How it works: High-speed gas jets break particles down through collision.
Example: Ideal for pharmaceuticals requiring micron-sized particles.
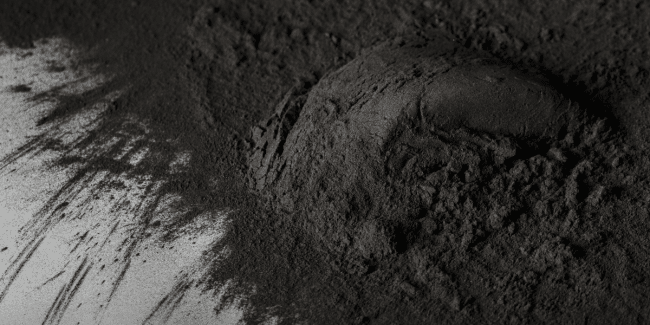
How to Improve Your Powder Milling Operations
With these powder processing methods in mind, let’s look at some simple tips to get the most out of your milling process.
1. Choose the Right Equipment
Not all mills are fit to do any job. The right choice depends on three factors: material hardness, desired particle size, and production needs.
Some materials need impact force, while others require shearing or compression. Using the wrong equipment can lead to inefficiencies or excessive wear — or worse, poor-quality output. Working with experts ensures you get the right setup from the start.
2. Control Process Parameters
Fine-tuning settings improves output:
- Speed & Feed Rate adjusted to balance throughput and particle size.
- Temperature Management prevents overheating sensitive materials.
- Airflow & Pressure (Jet Milling) optimizes particle breakdown.
Keeping tight control over these factors reduces variability and helps maintain consistent results across production runs.
3. Proper Pre-Milling Preparation
Now that you know how to fine-tune your milling operations, the next step will be proper pre-milling preparation. Here’s how getting your materials ready before milling can make a big difference:
- Drying reduces moisture-related clogging issues.
- Pre-crushing speeds up processing of large particles.
- Screening removes oversized or foreign particles.
Skipping these steps can cause process slowdowns, clogging, or inconsistent particle sizes. A little preparation upfront saves time and prevents costly rework.
4. Reduce Energy Waste
Wasting energy increases costs. Some milling processes consume more power than necessary due to poor equipment choices or improper settings. Using mills designed for bulk processing, maintaining sharp milling tools, and optimizing batch sizes helps cut waste. Efficient milling setups lower operational costs and improve overall throughput.
Wasting energy increases costs, but there are ways to cut down on unnecessary power use.
For example, using mills designed for bulk processing helps avoid overworking your equipment. Another way is keeping milling tools sharp to reduce friction, allowing the mill to run more efficiently and use less power.
Optimizing batch sizes also plays a role; processing smaller batches can take longer and use more energy, while larger batches are usually more efficient.
Consider Outsourcing to a Toll Processor
Managing in-house milling operations takes time, expertise, and costly equipment. For many businesses, outsourcing to a toll processor is the best way to get high-quality results without the investment. Instead of dealing with the complexities of powder milling, you can rely on a specialized partner like M&M Milling to handle it for you!
Industry Insights: The Impact of Proper Milling
A study in industrial powder processing found that optimized milling techniques can reduce energy use by up to 50% while improving yield consistency. Businesses that implement proper milling strategies also experience:
Benefit | Impact |
Reduced Processing Time | Faster production cycles |
Lower Material Waste | Higher product yield |
Improved Consistency | Uniform particle sizes |
Energy Savings | Lower operational costs |
Get Expert Milling Solutions with M&M Milling
Outsourcing milling to a toll processor like M&M Milling ensures access to specialized milling equipment, expert insight, and cost-effective solutions without the need for in-house investment.
Why Choose M&M Milling?
- Advanced milling technology for precise particle size control.
- Custom toll processing solutions tailored to your materials.
- Scalable capacity for small-batch or high-volume production needs.
Need powder milling solutions for your business? Contact us today to discuss your milling needs and improve your production process.