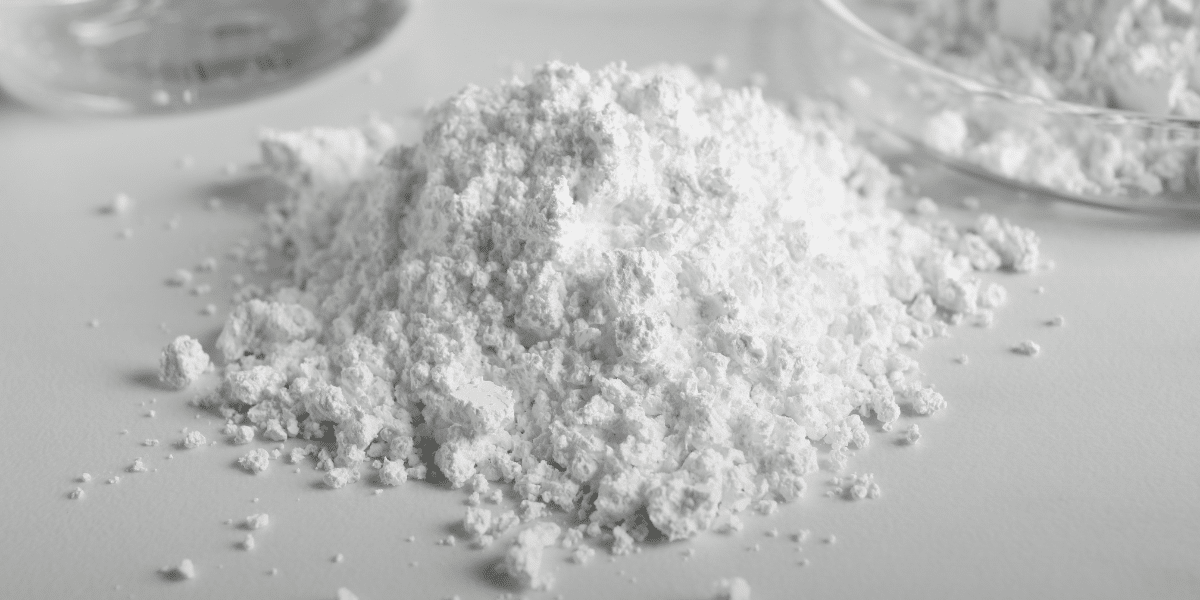
Pulverization vs. Milling: What’s the Difference & When to Use Each?
Processing raw materials often means breaking them down into smaller pieces. But not all size reduction methods are the same. Pulverization and milling are two common techniques, each with its own purpose and process.
What is Milling?
Milling is a controlled mechanical process that reduces material size through grinding, crushing, or shearing. It plays a big role in industrial applications where consistent particle size is required for processing, mixing, or product performance. Unlike pulverization, which focuses on ultra-fine powders, milling allows for a range of particle sizes, from coarse granules to fine powders, depending on the method used.
Different milling equipment and techniques apply varying levels of force, speed, and precision to achieve the desired result. The choice of method depends on factors like material hardness, required particle size, and downstream application.
Common Milling Methods:
- Air Classifying Milling uses an internal classifier to separate fine particles while returning larger ones for further milling.
- Ball Milling uses rotating balls inside a chamber to grind material into fine powder.
- Roller Milling uses rollers to crush materials into uniform sizes.
- Jet Milling uses high-speed gas streams to break particles into ultra-fine powders.
Expert Insight: The right milling technique depends on more than just particle size. Factors like material moisture content, flow characteristics, and reactivity all influence the process. For example, jet milling is often preferred for pharmaceuticals because it prevents heat degradation, while roller milling is ideal for bulk material production due to its efficiency.
What is Pulverization?
Pulverization is an advanced form of size reduction that breaks materials down into ultra-fine powders. Unlike standard milling, which focuses on reducing particle size, pulverization pushes materials to their smallest possible form, often on a micron or even nanometer scale.
This process relies on intense forces (high-speed impacts, pressure, or turbulence) to fracture particles beyond what traditional milling can achieve. Methods like jet milling and air classifying milling are used for pulverization because they apply extreme energy while controlling particle size distribution.
Expert Insight: Industries like pharmaceuticals and battery manufacturing rely on pulverization to achieve precise material properties. For example, active pharmaceutical ingredients (APIs) must be reduced to sub-micron sizes to improve absorption, while battery materials need tightly controlled particle sizes for better conductivity and performance.
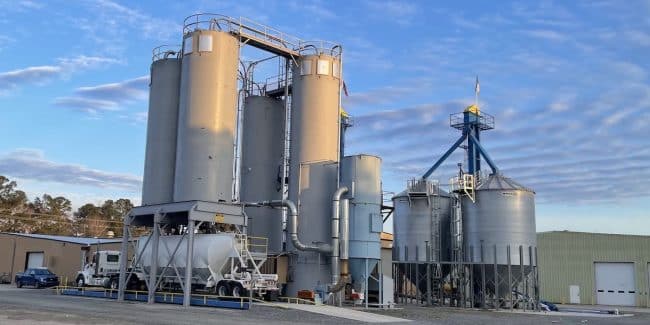
Q&A: Which One Should You Use?
Q: When should I use milling?
A: If you need consistent particle sizes but don’t need extreme fineness, milling is the way to go. It’s great for materials like grains, minerals, and plastics.
Q: What about pulverization?
A: Use pulverization when you need ultra-fine particles, especially for high-tech applications like medicine, batteries, or specialized chemicals.
Q: Can a material be both milled and pulverized?
A: Yes, some processes start with milling to reduce size, then use pulverization to get an even finer powder.
Think About End Use
Before choosing a process, consider how the material will be used. Need a smooth, even texture? Milling might be enough. Need fine powders that dissolve easily? Go with pulverization.
If you’re unsure, working with an experienced toll processor can help you get the best results without investing in expensive equipment.
Custom Solutions & Hybrid Approaches
Some materials need both milling and pulverization to get the right size and consistency. A hybrid approach can improve efficiency, cut costs, and meet strict quality control standards.
When to Use Both
- Pharmaceuticals: Coarse milling first, then micronization for better absorption.
- Batteries: Milled first, then pulverized for precise particle size.
- Food Processing: Milling for bulk reduction, then finer grinding for better texture.
Key Factors to Consider
- Hardness: Tough materials may need pre-milling.
- Moisture: Wet materials may need drying between steps.
- Final Use: Particle shape and size impact performance.
A trusted toll manufacturer like M&M Milling can customize processing to fit your needs.
Learn More from M&M Milling
Need help deciding between pulverization and milling? M&M Milling has the equipment, experience, and expertise to handle your toll processing and material handling needs. Get in touch with our team today to discuss your project and see how we can help streamline your operations.